Epoxy and Industrial Flooring
Performance Industrial Guide to Epoxy and Industrial Flooring
Epoxy is a term that represents a class of materials and the act of using those materials. Our guide to epoxy and industrial flooring includes information epoxy “systems” which are based on a combination of resins and hardeners. When mixed together, the resin and hardener chemically react to form a rigid plastic material. The final material is strong, durable, resistant, and bonds extremely well to most base layers. Epoxy floors are so strong that they are ideal for heavy traffic areas such as industrial locations, hospitals, universities or sports facilities. New construction, epoxy floor repairs, or specialized designs, Performance Industrial will customize our seamless, industrial flooring systems to meet your specific needs. We work within your schedule with focused attention to detail. Each of our flooring experts has more than 20 years experience and provides exceptional workmanship. Our epoxy flooring systems are easy to clean and maintain and can be installed over existing coatings or used to resurface old or worn concrete. Our seamless flooring systems are available in a variety of colors and designs with a choice of finishes such as matte, satin, high-gloss, and slip-resistance. If you’ve ever considered an easy-to-maintain, industrial-grade flooring option, we bet there’s an epoxy solution for you! Epoxy is a unique solution because it’s not only incredibly practical, but the materials used in it make it flexible for almost endless applications. From creating beautiful entrances for hotel lobbies to fire-proof warehouse flooring, there’s an epoxy system for you.
Types of Epoxy Flooring Systems
At Performance Industrial, we offer over 30 different epoxy and industrial flooring systems. Here are a few of our most popular:
Self-Leveling Epoxy Floors
Self-leveling epoxy is applied over new, old, cracked, or damaged concrete floors to create a smooth, seamless, durable, and low maintenance flooring surface. The self-leveling system is also available in a variety of colors. Colors are used to make decorative designs, denote traffic patterns, or highlight work zones in industrial settings. This system is used when you need aesthetic appeal and/or abrasion, chemical, heat or slip resistance.
- Where we’ve used it: Manufacturing facilities, warehouses, showrooms, commercial garages, kitchens, aircraft hangars, athletic facilities, and more.
Epoxy Mortar Floors
Ultra-tough, this is the strongest epoxy floor system available. This high-build, seamless system is made with 100% solids epoxy and graded sand or quartz sand and then troweled into place. Mortar systems are highly impact and chemical-resistant. This system is also effective in repairing old floors because of its high-build process.
- Where we’ve used it: Manufacturing plants, mechanical rooms, warehouses, commercial kitchens, restaurants, garages, and service areas where heavy equipment, such as forklifts, would be used.
Quartz-Filled Epoxy Floors
Quartz epoxy flooring systems combine high-performance epoxy polymer resin with colored quartz grains. The result is a multi-functional floor that’s decorative, sanitary, slip-resistant, and exceptionally durable.
- Where we’ve used it: Locker rooms, restrooms, schools, cafeterias, showrooms, light manufacturing, lobbies, offices, and more.
Anti-Static Epoxy Floors (ESD Resistant Floors)
Electro-static charge (ESD) can be extremely dangerous in many work environments. Anti-static epoxy flooring helps to reduce static hazards. This flooring system typically contains a conductive material that accumulates static electricity to drain, ground, or dissipate any potential discharge. It’s highly recommended in environments that contain flammable materials.
- Where we’ve used it: Healthcare facilities, electronic, chemical or pharmaceutical manufacturing facilities; areas that use flammable gases or liquids or risk combustible dust buildup.
Epoxy Flake Floors Flake floor systems are made when colored chips or flakes are placed within the epoxy to create vibrant, multi-hued, seamless, resilient surfaces. The chips are not only aesthetically pleasing, but their slightly rough surface reduces slips and falls. The flakes are available in an endless variety of colors, styles, textures, and sizes and can be mixed into the combination of your choice.
- Where we’ve used it: Commercial kitchens, locker rooms, sports venues, automotive showrooms, veterinarian clinics, laundromats, and more.
5 Reasons to use Epoxy Flooring
When facility managers or others in similar positions come to us around repairing their concrete floors, they’re most often concerned with aesthetics. But, there are actually 5 important reasons to renew and resurface the floors in your commercial or industrial facility.
1. Customer Safety
Employees are far more likely to suffer trips, slips, and falls if your floor is cracked, pitted, or uneven. Concrete floor repair and epoxy polyurethane floor coatings are an essential step to help keep this from happening. Concrete repair floor coatings with a textured, skid, and moisture resistant epoxy will further enhance your floor’s safety and make it safe for your customers and employees. These safety considerations extend to your parking garage as well:
- Customers’ vehicles are more likely to lose traction in a parking garage that isn’t maintained properly as traffic wears down the surface over time.
- The material applied to the surface is rough when you seal your parking area, which improves the friction between the surface and your customers’ tires.
- Customers don’t know where to park when a parking lot has faded paint, often leading them to park their vehicle wherever it seems most convenient, taking up more space than necessary and causing problems when the next customer looks for a spot.
- When customers can clearly see parking spaces, they know exactly where to park, and what areas are off limits. Adding arrows to show proper traffic flow can prevent confusion and significantly improve traffic flow.
- Striping also improves safety. Reflective paint stands out even at night, and direction arrows help drivers avoid collisions with one another.
2. Environment
Cracked floors and trenches may be allowing hazardous chemicals to seep into the ground below. Not only is this environmentally unsound, but it likely violates EPA regulations. A well-kept floor with secondary containment can help prevent this. Epoxy Coatings for Secondary Containment
- According to the EPA, industries where oils, chemicals and other hazardous materials are present must have a secondary containment systems in place in the event of a leak or spill.
- Depending upon the industry, a secondary storage system can consist of portable storage containers mounted on pallets off the floor. However, if a spill occurs, there must be enough secondary containment systems on hand to hold the entire contents of the spill.
- Before coating your secondary containment system, you will need to work with a coating specialist who will assess the condition of the flooring and sides of the walls before sealing them. The specialist will assess the overall condition of the flooring to ensure there are no cracks, fissures or seams where spillage could accumulate and seep into the substrate.
- If your flooring is already sealed with an epoxy coating, it is important to make sure that it is still impermeable and has the ability to withstand an oil or chemical leak. If your existing facility was not originally built to accommodate the existing processes and materials, you may need to remove and replace the existing sealant.
- Your flooring and sealing specialist may recommend shot blasting and grinding to remove the old coating and replace it with a material that is compliant and will be able to handle containment in the event of a leak or spill. It is required that the containment area must contain the spill for at least 72 hours.
- Once any necessary remediation work has been completed, you can install a system of berms that will separate and contain any leaks or spills and allow you to get the situation back under control without any contamination or harm to the facility.
In New York State, containment areas are monitored by the New York State Department of Environmental Conservation (NYSDEC), and Performance Industrial has a NACE certified coatings inspector with over 20 years of experience.
3. Longevity & Durability
Cracking and pitting are signs of aging concrete. Once they start, they expedite the deterioration of your floor. Keeping the cracks at bay with regular maintains helps ensure your money is well spent.
4. Cleanliness
In many warehouses, quality control depends on strict cleanliness standards. Concrete dust can make meeting these standards nearly impossible. Floor repair and regular coating updates can prevent dust, optimize production, and make cleanup easier in any facility.
5. Aesthetics
Yes, how it looks is still important. Stained, cracked concrete shows lack of attention and professionalism – especially if in an area your customers can see. But, what you may not have considered, is that the way your facility looks influences how your employees feel as well. Maintain a place someone is proud to work for and everyone will be amazed at the difference it makes! No Boring Flooring! If aesthetic appearance is an integral component of your business, epoxy flooring can offer a range of colorful, dramatic and beautiful solutions. Our high gloss surfaces can add sophistication and decorative flair to showroom floors, retail spaces, atria and other locations where appearances are everything. In addition to beauty, they are durable, long lasting and easy to clean and maintain. Our professional team of industrial flooring experts will come to your facility to perform a complete hazard assessment of your existing flooring, and offer the right solution for your business or facility’s needs. New flooring will result in better performance, reduce or eliminate the risk of exposure to environmental contaminants, and dramatically improve the appearance of your facility. With more than 20 years of experience under our belts, we can offer the kind of professional advice and expert repairs and installations you need to get your facility up to standards and looking great!
Installing A Commercial Epoxy Floor: What You Need to Know
Epoxy floors and coatings are ideal when you need practical durability and long-term solutions. The seamless systems make them easier to clean, sanitize, and reduce necessary maintenance and upkeep. There are dozens of possible materials and an infinite number of combinations of epoxy systems, however, finding the right solution can feel overwhelming. Your contractor should be there to help…if they’re asking the right questions. Whomever you hire, we wanted to share the list of questions we ask to get to the solution you need. Feel free to use these questions as a guide to start a meaningful partnership with your commercial or industrial contractor. Have you heard these questions from your epoxy contractor? Does your floor need to withstand:
- Heat
- Tire marks
- Extreme weight
- Heavy traffic (hundreds, or thousands of people?)
- Chemical spills
- Frequent cleanings
Will your floor need to be:
- Anti-microbial
- Eco-friendly
- Slip resistant
- Stain resistant
- Shock resistant
- Static resistant
- Impact and abrasion resistant
Are you looking to:
- Include in-laid graphics or logos
- Highlight traffic patterns
- Identify safety areas
- Enhance the aesthetics of the space
Will you be using the floor in a space for:
- Athletics
- Food preparation
- Lab work (clean rooms or research)
- Dining
- Automobiles or planes
- Bathing
- Surgery
- Chemical containment
- Machines or equipment involving electricity
- Forklifts or steel carts
- Pools or patios
- Animals
Does your vendor know about:
- Epoxy and MMA
- Poly aspartic, polyuria and polyurethane systems
- Concrete or Ardex systems
- Primers for moisture mitigation, vapor pressure or hydrostatic pressure
Do you know:
- The dimensions of your space
- What the average temperature is – does it fluctuate frequently or by large amounts throughout the year?
- How old your substrate layer is
- If concrete is your substrate, was it recently poured? Is it smooth or sealed? What type of curing agent was used?
- If it’s a humid environment
- If the space ever had oil, grease, or salts in it
- If there is a drain present
- How quickly you need to use the floor after installation
- If the space will be occupied during this work
- What your expected lifespan is for this floor
- What your budget is
Every space is different and unique touches can make or break your epoxy floor installation. Before starting any flooring work in your commercial, industrial, or institutional facility, consult these questions to help ensure that you get what you need from your epoxy contractor.
Guide to Epoxy & Industrial Flooring Troubleshooting
Installing epoxy floors can seem like a simple project. Prepare the surface, prime your substrate (base), create your epoxy mixture, pour. However, when you’re dealing with expansive spaces and varying environments, a number of costly mistakes can occur because of improper assessment and preparation.
Blistering, Bubbling, and Bad Bonding in Epoxy Floors
The truth is: epoxy floors are a science. Like any science project, you have to look at all of the variables – the temperature, humidity, ingredients, time, materials, tools, and more. If one piece is off balance, the final product can suffer. Thankfully, experience in the field has helped us prepare for almost any scenario. When customers ask us to assess their current epoxy floors, here are some of the errors we’re on the lookout for: Bubbling Bubbling occurs when air is trapped beneath the surface of the epoxy layer. Two things happen here scientifically and both have to do with temperature: 1) If the coating is exposed to direct sunlight and warms, the air underneath will expand and try to escape, pushing the layer upward and causing a bubble; 2) If the coating is applied in a cool or cold room and the temperature changes later on, trapped air will rise and cause a bubble. Blistering Blistering happens when liquids pass through the “membrane” created by the epoxy coating, like osmosis. Liquid builds up on the underside of the coating and tries to evaporate, or push up. The moisture-resistant epoxy prevents it from escaping and causes a blister. Bad Bonding The successful building of your epoxy floors is dependent on the bond it makes with the substrate below it. Odds are, improper floor preparation is the culprit if you see cracking, peeling, separation, discoloration, or overall lackluster results.
How do we prevent problems?
The skills needed to apply epoxy can set one contractor apart from another. However, the success of your long-term investment truly relies on the process – what happens before installation to guarantee it will work? Assess the Environment:
- Moisture and Temperature: Solvent-based epoxy products do not bond with humidity and applying epoxy over floors that “sweat” are an all around bad combination. We assess the entire project to make sure it will be possible to make a completely dry environment for application. The temperature in the room can also affect moisture and cause it’s own category of problems.
- Substrate: Your house is only as good as your foundation, right? Your epoxy system works the same way. That’s why we strive to understand what’s happening underneath. Wood floors can bend and flex, cracking epoxy. Low-quality cement can trap air or erode over time and cause a bad bond, blisters, or bubbles. A thorough assessment of your substrate layer will determine if epoxy is the right solution for your needs.
- Preparing for Installation
- Cleaning
- If there’s one major lesson to learn, it’s here: cleaning. The chemical reaction needed to make epoxy successful is dependent on an environment free of contamination. We recommend a proper cleansing, shotblasting, grinding, and preparation sequence to remove dust, oil, grease, salt and more that can interact with your final product. It is important to create a rough profile, or opening the concrete pores, to ensure proper penetration and adhesion of the floor system.
- Priming
- If you’re choosing epoxy for your flooring system, we can guess that you need something that can withstand heavy wear and tear. The more you protect the substrate, the better your results will be. Proper understanding of industrial primers and how they interact with your specific epoxy is critical.
- Industrial primers should also be selected based on the particular environment. Vapor pressure, moisture, temperature, hydrostatic pressure and more can all lead to different decisions and priming solutions.
- Mixing
- Epoxy coatings are created when resin and hardener chemically react to form a rigid plastic material. We pay special attention to time spent mixing, the size of the batch, the environmental conditions, and the ratios and equipment used to make sure all of your careful preparation doesn’t go to waste because of a bad mixture.
Moisture Vapor Emission from Epoxy Floor Coatings
Even the most carefully poured flooring can have unacceptable rates of moisture emission from epoxy floor coatings, which can undermine the integrity of existing floor coatings or make it impossible to install new epoxy flooring that will withstand the moisture levels. Here are some questions that we get about preventing and addressing epoxy floor moisture vapor emissions in commercial and industrial applications: “What are the steps I should take before moving ahead with installation of an epoxy coating?”
The most important and prudent measure to take before installing a floor coating system is to take a measurement of the moisture vapor emission rate (MVER).
“How do I measure the amount of moisture vapor emission from epoxy floor coatings coming from my concrete flooring?”
The two main tests to determine the MVER are the calcium chloride test and the relative humidity test.
1. The first method involves the placement of pre-weighed calcium chloride containers sealed with plastic coverings at 1,000 square-foot intervals. The calcium chloride crystals in the container are weighed again after 72 hours to determine the amount of moisture that has been absorbed.
2. The second method requires drilling holes in the substrate and inserting probes to measure the levels of moisture below the surface of the flooring. This second method is perhaps the better of the two and provides a more accurate assessment of the true level of moisture at a deeper level.
“My concrete flooring was installed years ago. Why would I have vapor emission problems now?”
Moisture issues can occur with both old and newly installed concrete. If concrete formulations had too much water, or if the concrete wasn’t properly cured, it doesn’t matter that the flooring has been in place for a long time.
Another factor that can contribute to higher levels of moisture vapor emission is the water table in the region. Certain areas of the country with higher water tables may result in higher moisture emission levels coming from your flooring
“What are the effects of high moisture vapor transmission on my epoxy coating?”
Concrete flooring that has been sealed using epoxy coating without first being tested for moisture vapor emission levels may require mitigation and repair down the road. The moisture will eventually undermine the surface treatment, resulting in cracking, chipping and – ultimately a total breakdown of the entire coating.
“What is the next step after I have determined the level of moisture vapor emission in my flooring?”
There are many products and processes available that will mitigate the moisture level issues in your concrete flooring prior to the installation of your epoxy coating. Working with a team of professional flooring installation specialists will ensure that your flooring is properly treated and the right coating technique is applied that will protect your investment.
The techniques used by the experts at Performance Industrial include captive metal shot-blasting, vacuum diamond grinding, sanding, scarification and hand-diamond grinding. Based on the unique situation and requirements of your flooring needs, the team will work together to determine which remediation solutions will be the most effective and what coatings will offer the longest life for your concrete floor.
For more information on the performance industrial guide to eat epoxy and industrial flooring, contact us directly at (518) 793-9274, or learn more about our commercial and industrial services. Performance industrial is a leader in industrial cleaning,HVAC cleaning, painting, sandblasting and Rapid Image Improvement.
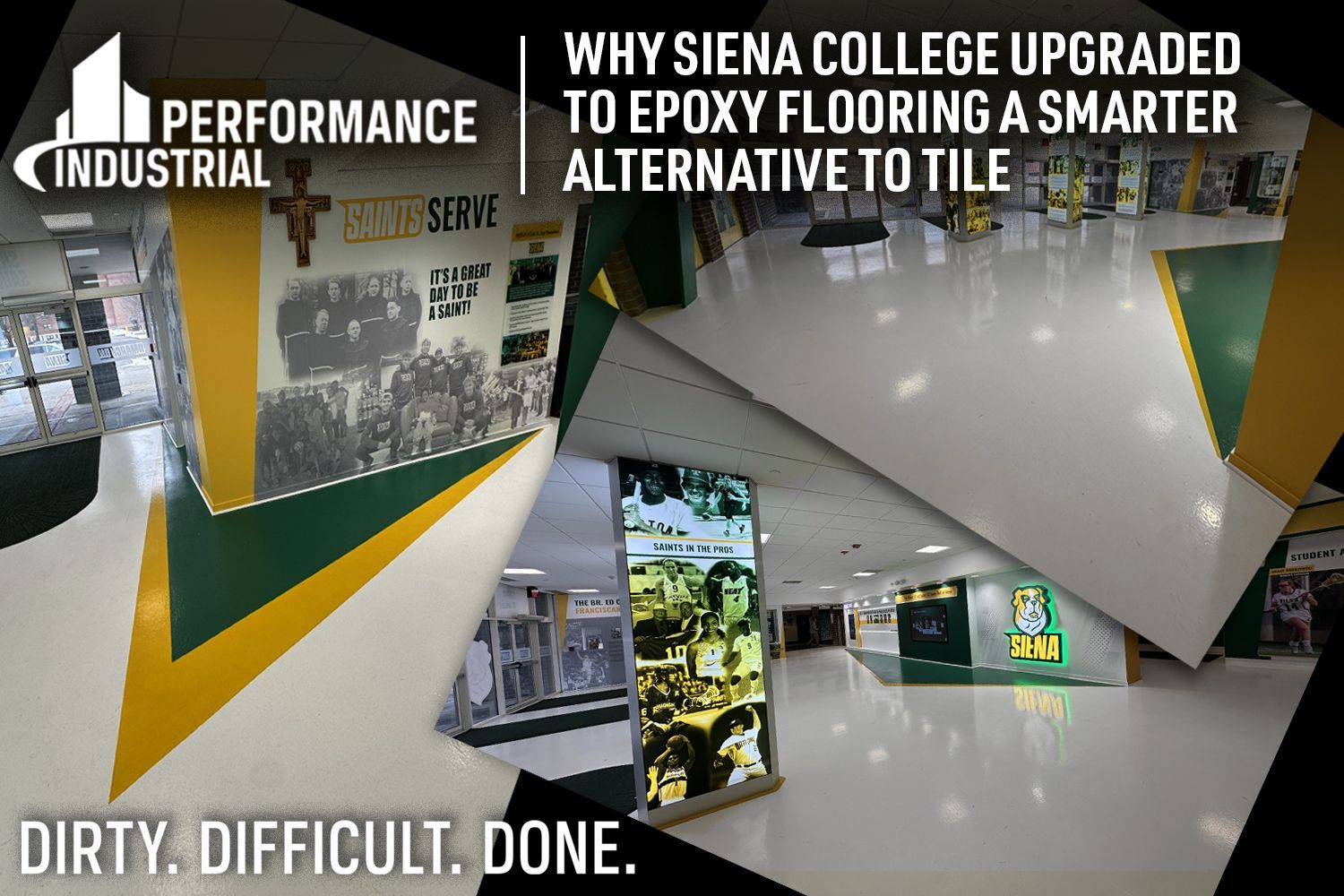
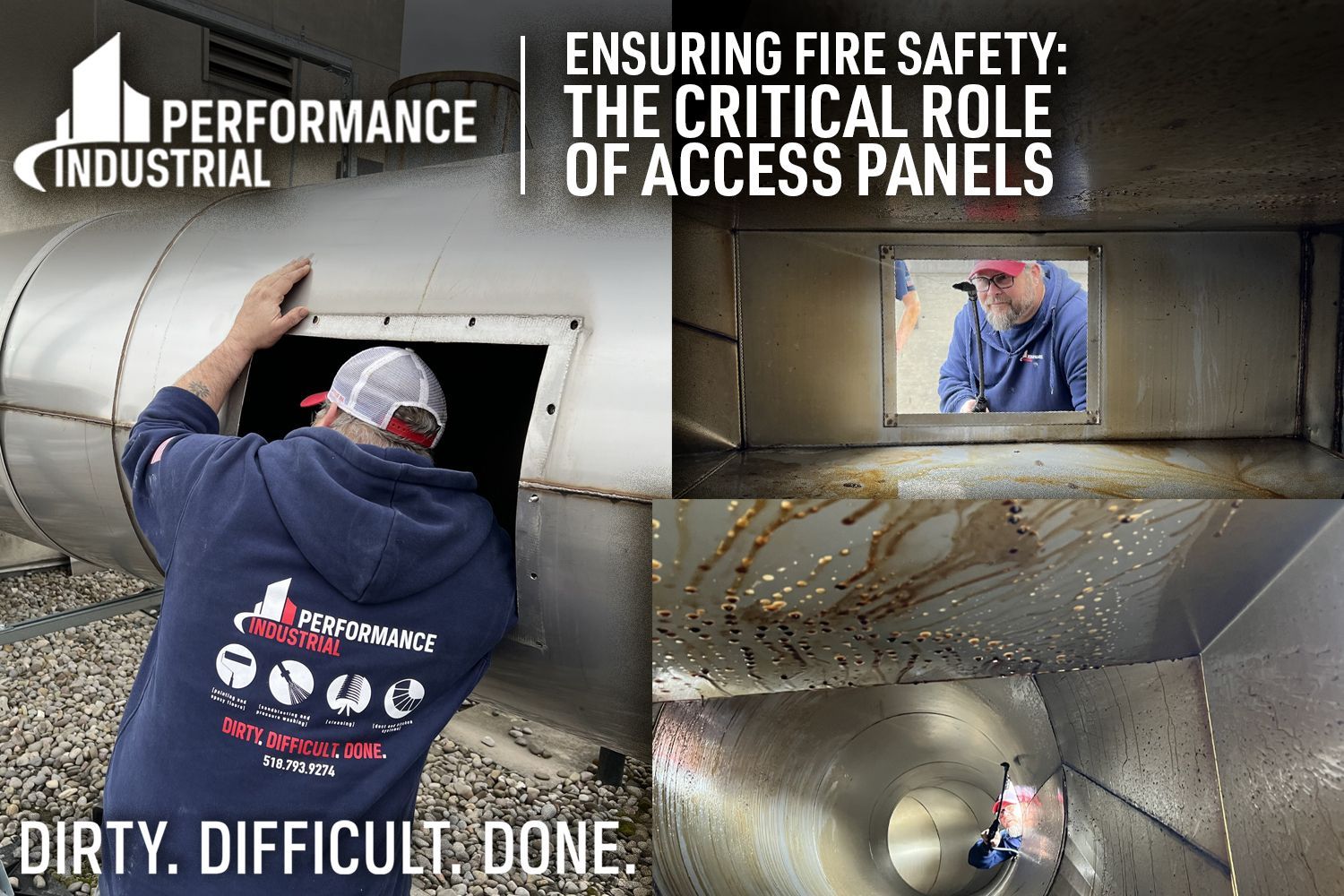
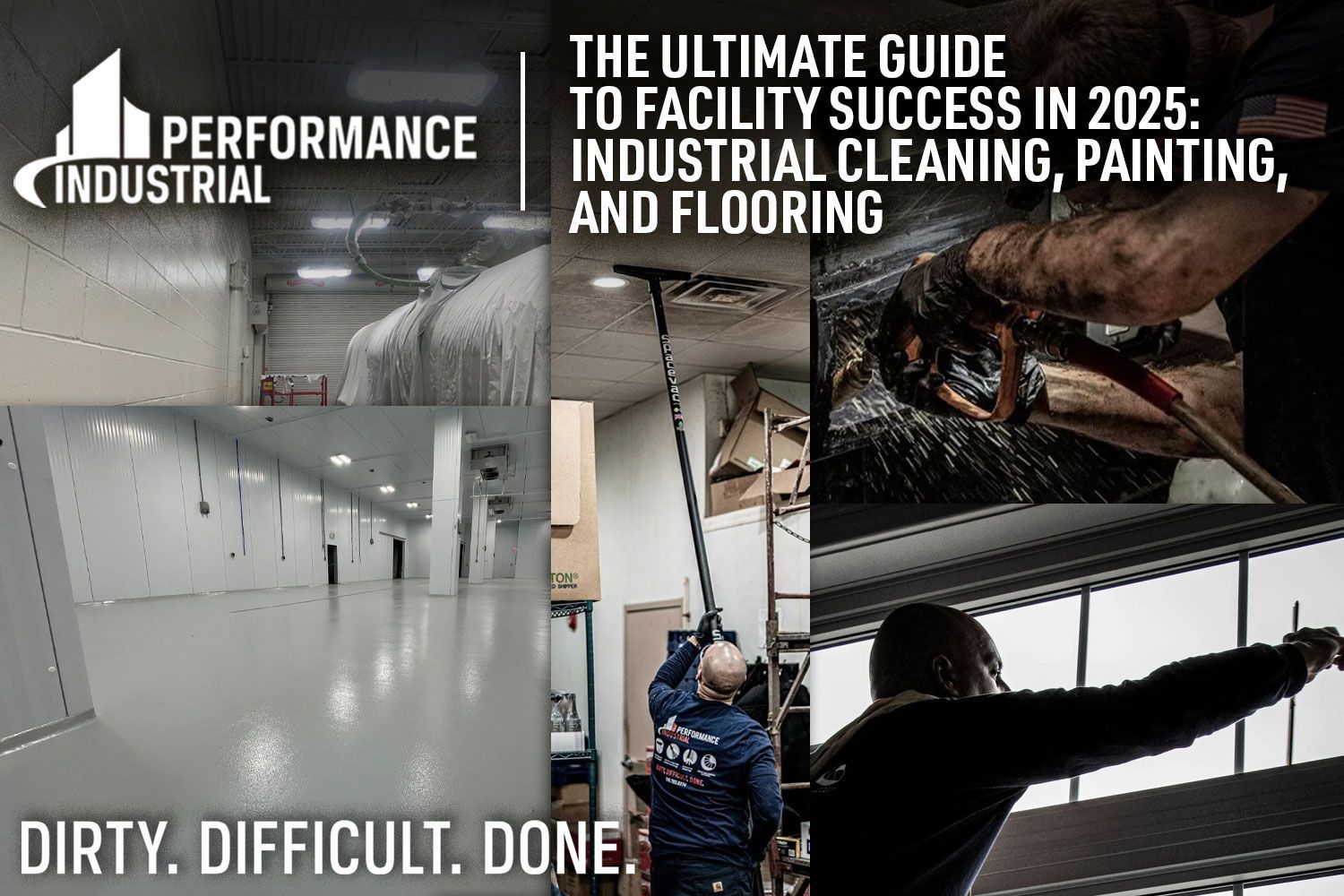
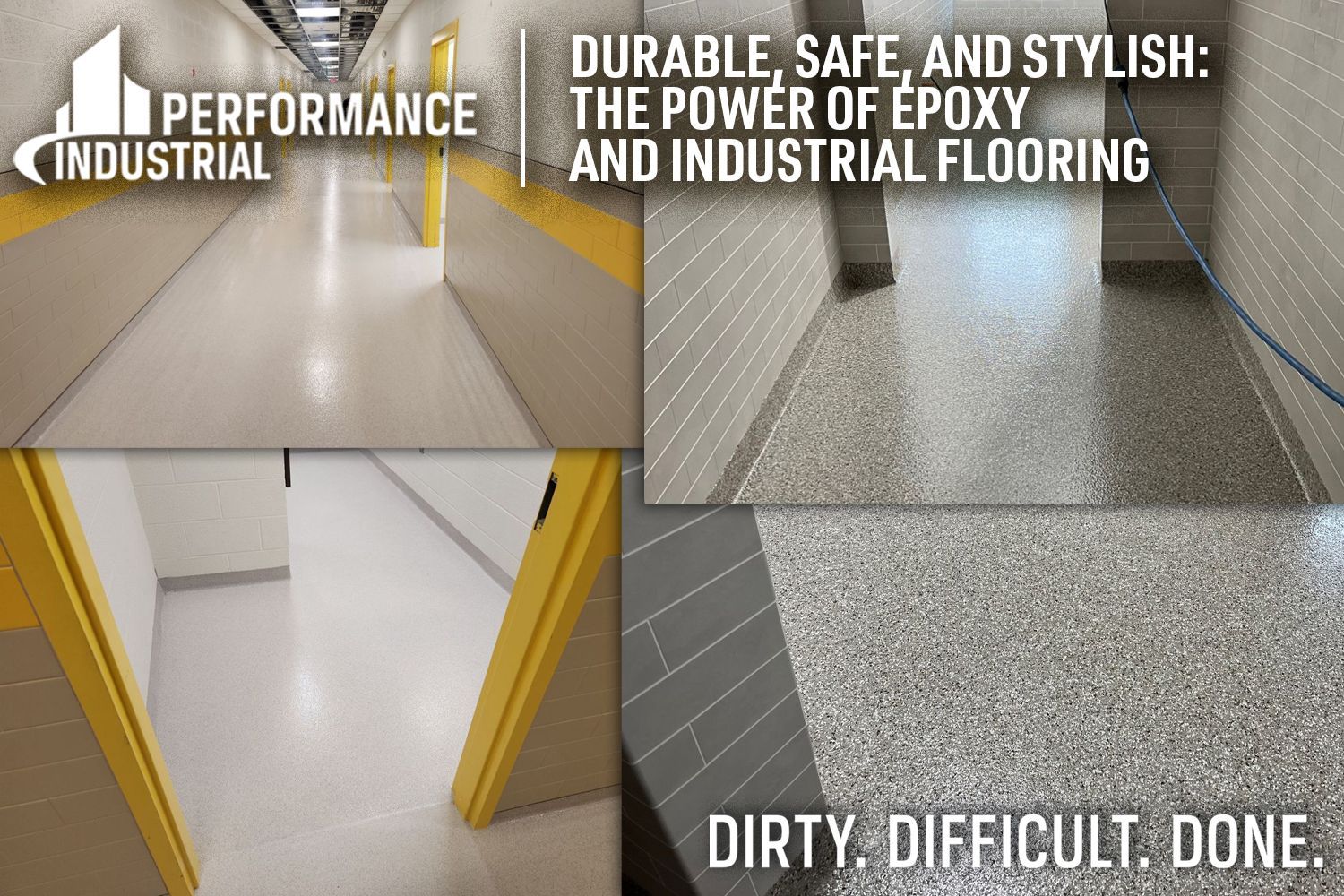
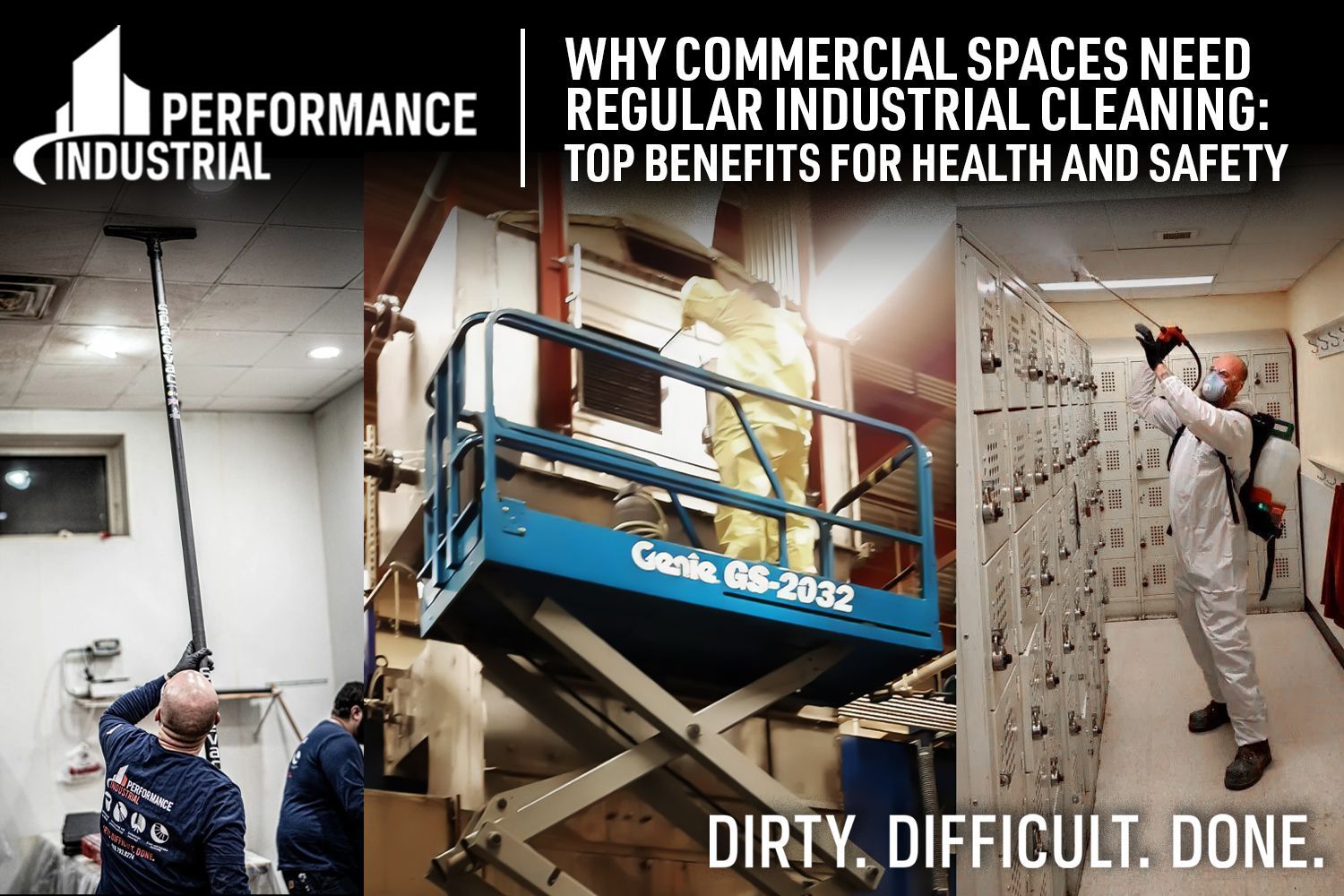
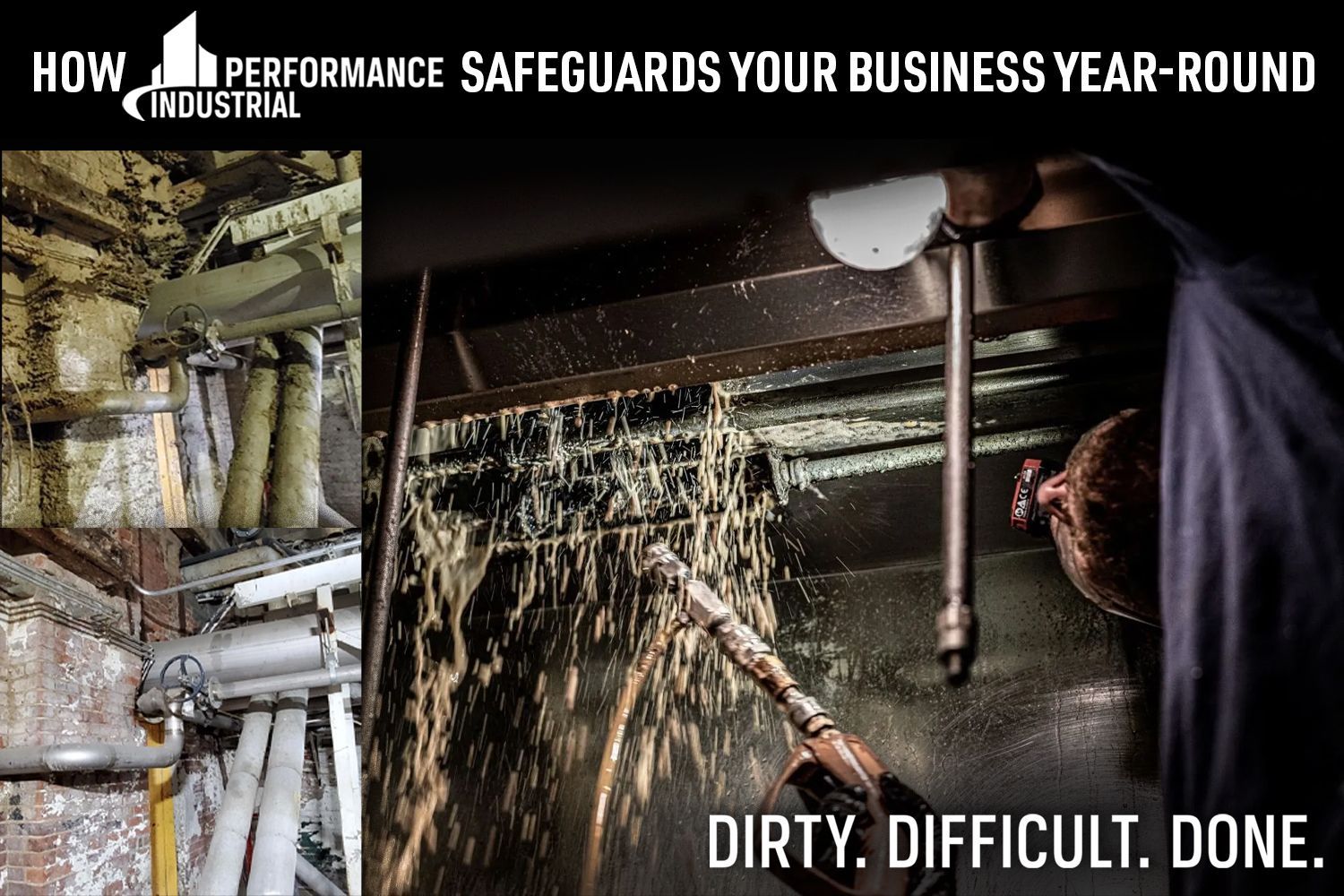
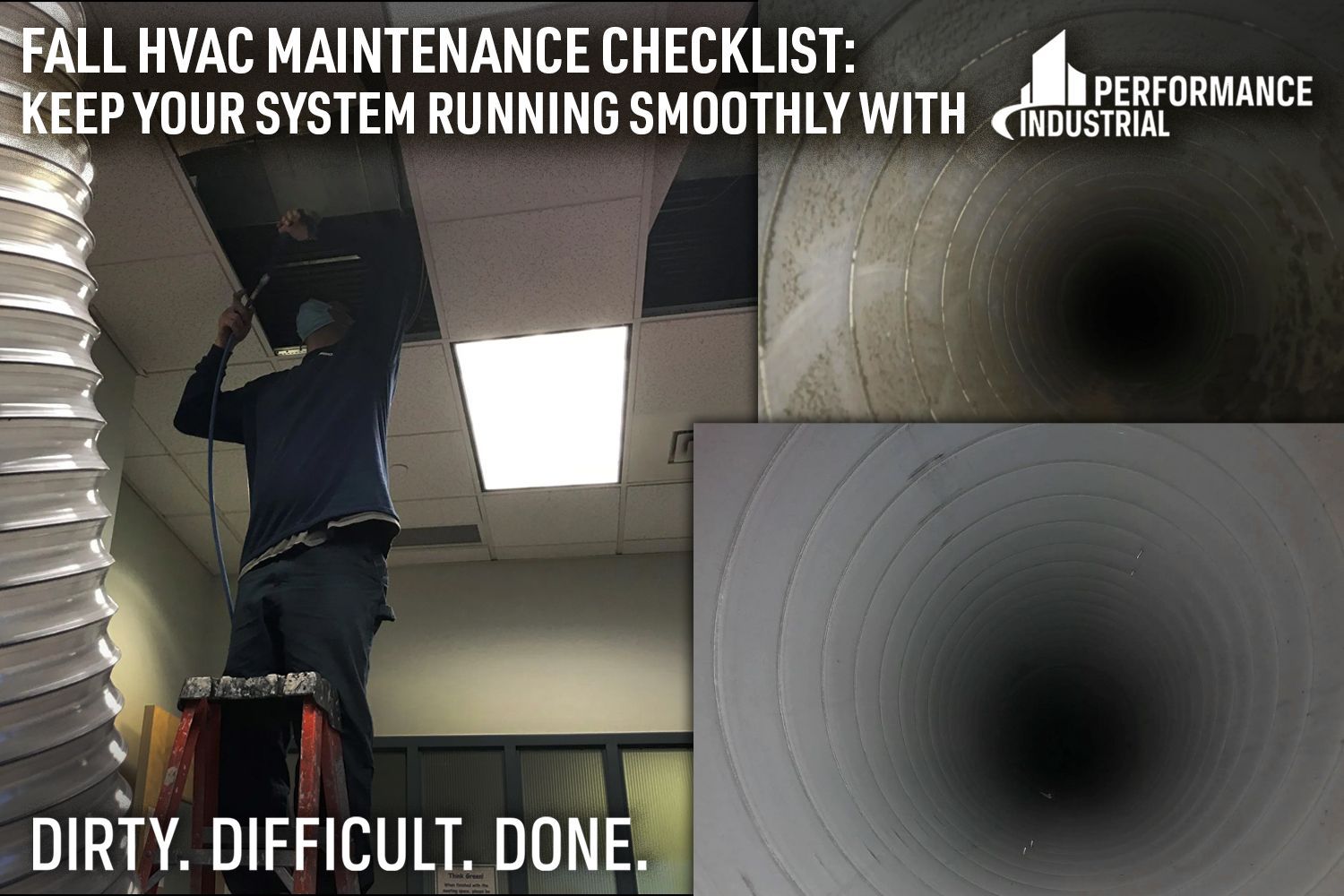
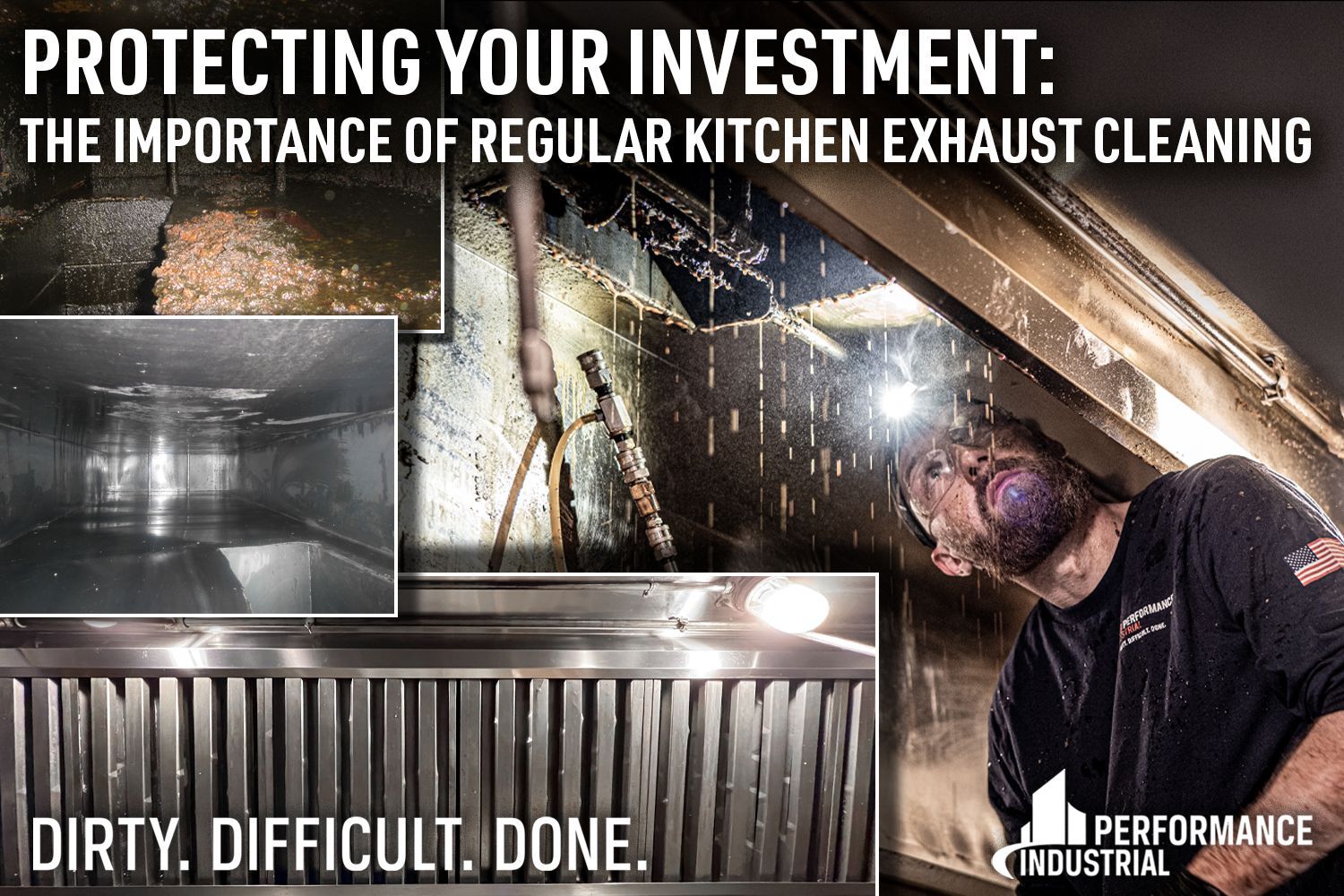